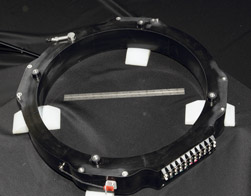
Everson Tesla has long supported the power generation industry, always utilizing innovative approaches to solve practical problems. Proven capabilities in design, material selection, prototype modeling, coil winding and insulation systems have placed Everson Tesla among the cutting edge suppliers for coils used in rotating field applications.
Transitioning from large DC stationary field coils and rotating fields for synchronous motors to highly reliable and efficient rotor coils for today's turbo generators exemplifies the manufacturing diversity that Everson Tesla has achieved over the past 75 years. A dedicated, multiple-shift facility has been established to meet the growing industry demand for these air-cooled and gas-cooled two and four pole rotor coil sets.
Everson Tesla currently supplies rotor coils, either insulated or not, in several configurations:
- C-PIECE
- CONTINUOUS WOUND
- SQUARE CORNER
New and replacement stator coil design
Computer design tools and specialized manufacturing tools enable us to provide customers with reliable coils of uniform shape. Coils can be insulated using one of Everson Tesla Incorporated's proven insulation systems or using the customer's insulation system when desired. Wire insulation available in enamel, dacron glass, kapton, and mica tape system supplied for coils over 7,000 volts.
New and replacement field coil design
Computer design tools and specialized manufacturing tools enable us to provide customers with reliable coils of uniform shape and size. Coils can be supplied without insulation or insulated using Everson Tesla Incorporated's proven insulation system or using the customer's insulation system when desired. Coils can be wound on field poles using round, square, or rectangular copper utilizing either wet winding techniques or VPI'd following winding. Strap coils can be continuous wound, brazed corners, or a combination of brazing and winding.
New and replacement stator coil manufacture
Specialized manufacturing tools and processes enable us to provide customers with reliable coils of uniform shape and size. Machine fed taping of slot portion of high voltage stator coil maximizes the effectiveness of the ground insulation. Computerized spreading of full loop coils assures uniform geometry. Surge and dielectric testing of coils during manufacture. Tan Delta and Partial Discharge testing of fully cured coils and bars to assure proper consolidation of coil insulation. High potential testing up to 75KV allows for destructive sample testing to assure quality processing of coils.
New and replacement field coil manufacture
Specialized forming, brazing, welding, and cutting processes enable us to provide customers with any size and shape of coil.
Specialized forming tools limit deformation in continuous wound coils eliminating the need to grind coils, which permits lower operating temperatures. Overlap, butt, scarf, mitered, and interlocking joints are available for brazing or TIG welding joints. Special fixtures allow precision cutting of joints required for butt welding joints into coils. Water jet cutting of copper plates creates any complex lead connections.